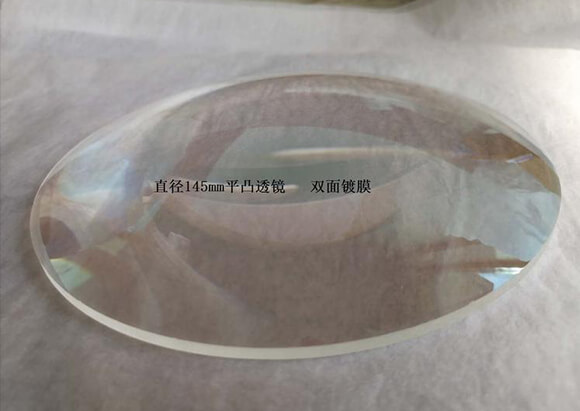
IR/DLC
IR coating refers to a coating in the infrared region of 2.5 μm (2500 nm) to 16 μm. There is a big difference between IR coating and near infrared coating in the choice of materials and manufacturing technology. They are mainly used in industrial and medical laser equipment, such as CO2 laser, Er:YAG laser, CO, HF laser.
The DLC coating window is a technique for forming plasma in a high vacuum state and coating the product surface with carbon as the main component of diamond, which is manufactured using PVD or CVD equipment. The DLC coating serves as a window to increase the transmittance in the infrared region, and is applied to products that require high durability and hardness on the surface exposed to the outside. By using a dielectric on one side of the DLC coating, it can show higher transmittance and continue to be a high-quality product for imaging applications.
Applications :
Product Advantage :
Intrinsic crystals provide DLC coating services for silicon, germanium or ZnS substrates according to the ISO 14577 standard. The typical coating wavelength of silicon is 3.0-14.0um, and that of GE and ZnS is 8-14um.
Product Parameters :
products and services.